Construction fences are essential components of any building site, serving as barriers that protect the project, the workers, and the public. When evaluating the total construction fence cost, several factors come into play, each contributing to the final expenditure. Understanding these elements is crucial for project managers and construction professionals who strive to balance safety, security, and budget constraints.
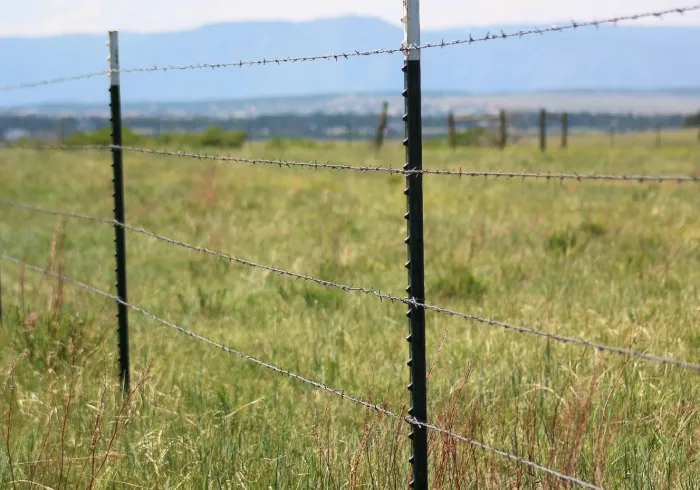
The primary consideration in assessing construction fence costs is the type of fence required. Different projects necessitate different barriers. Temporary chain-link fences are popular due to their robustness and flexibility, ideal for most large-scale sites. They are affordable and provide a decent level of security. However, for high-risk areas or sensitive locations, solid hoardings are often used. These offer greater privacy and security, shielding the site from onlookers and potential intruders. The cost for these sturdier structures tends to be higher, reflecting the additional materials and labor requirements.
Another critical factor is the length and height of the fence. Naturally, a longer fence requires more materials and labor, increasing the cost. Height is another consideration; while a standard construction fence might be six feet tall, certain sites may require taller barriers, especially in urban environments where taller fences not only provide security but also help reduce noise pollution. Each additional foot in height can significantly increase the cost due to the need for added materials and structural support.
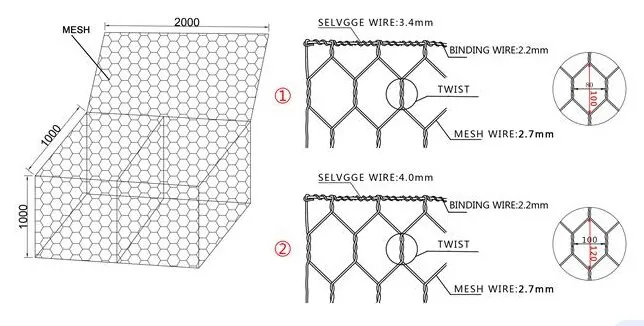
Material selection impacts the overall cost significantly. While chain-link is more economical, other materials like wood, steel, or vinyl might be employed depending on the project’s specific needs. While wood provides a more aesthetically pleasing appearance, it can be more costly to install and maintain, particularly in adverse weather conditions. Steel, while durable, is heavy and requires skilled labor to install properly, influencing labor costs. Conversely, vinyl, while durable and easy to maintain, can be more expensive upfront but may save money in maintenance over time.
Installation costs are another critical component. Depending on the terrain and the complexity of the installation, labor costs can vary widely. A flat, unobstructed site will naturally be cheaper to fence than a rocky or unstable area that requires additional groundwork. Moreover, urban sites may incur higher costs due to logistical challenges such as restricted access and the need to work within local regulations.
construction fence cost
Permits and regulations can also affect the total cost. Many regions require specific permits for temporary fencing, necessitating an understanding of local legislation and potentially involving further expenses to ensure compliance. Failure to adhere to these regulations can result in fines or project delays, underscoring the importance of incorporating these considerations into the initial budgeting process.
Renting versus purchasing fences presents another cost consideration. For short-term projects, renting can be more cost-effective as it eliminates maintenance and storage concerns. However, for ongoing or long-term projects, purchasing might be the better financial decision, allowing the company to amortize the cost over multiple projects, leading to savings in the long run. It’s essential to analyze the projected duration of use when considering these options.
Beyond the mere financial aspects, choosing the right construction fence involves considering the intrinsic value of safety and security. A well-selected and maintained fence not only protects valuable equipment and materials from theft and vandalism but also ensures compliance with safety regulations that shield the workforce and the public from potential hazards. Ignoring these safety aspects can lead to costly breaches, both financially and reputationally, compromising future business opportunities.
Environmental considerations are emerging as another factor influencing construction fence choices. Sustainable construction practices are increasingly popular, with companies seeking to reduce their carbon footprint. Fences made from recycled materials or those that can be repurposed after use are gaining traction in the industry. While these options might initially appear more costly, they can enhance a company’s reputation and viability in increasingly eco-conscious markets.
In conclusion, calculating the construction fence cost involves a detailed examination of various impacting factors. By understanding the type of fence needed, material choices, installation complexities, regulatory requirements, and the decision between renting and purchasing, businesses can make informed choices that align with both their immediate project needs and longer-term strategic goals. Emphasizing safety, compliance, and sustainability not only mitigates risks but also elevates the company’s status as a responsible and forward-thinking industry player.